Humbel Zahnräder AG
Optimal machine uptime with a positive impact on capacity, logistics, storage, and delivery times
Minimizing time to output: set-up workshops at Humbel Zahnräder
Set-up time always means production downtime. Optimization can lead to time savings of more than 50 percent. At the same time, savings are made in logistics and storage. Set-up workshops carried out by Ingenics at Humbel Zahnräder AG in Kradolf, Switzerland, area are prime examples of these cost reduction efforts. With no significant investment, it is now possible to align the production of high-quality gears much more effectively to customer needs.
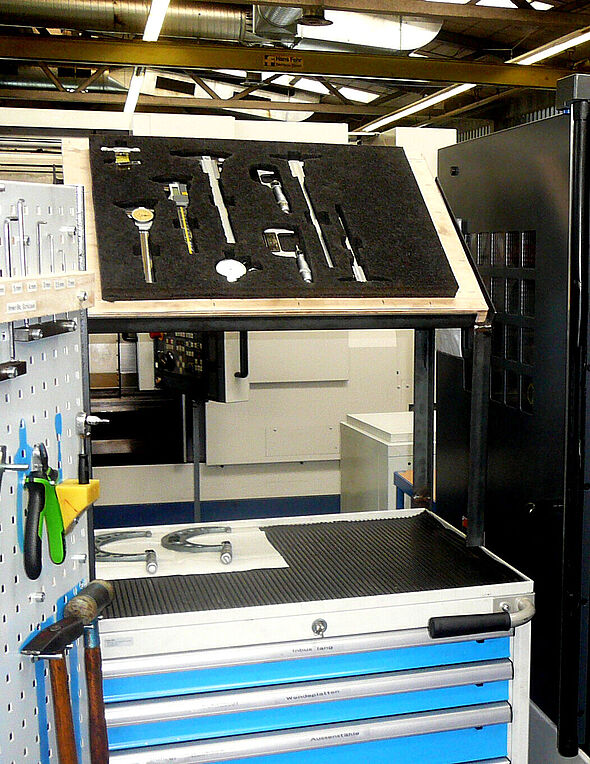
- Set-up times reduced by about 50% by cutting material and tooling search and access times and shortening travel distances
- Reduced batch sizes, logistics costs, and storage capacity by up to 60%
- Space savings
Optimizing set-up processes in production leads to an increase in productivity by allowing more flexible systems, smaller batch sizes, responsiveness to specific customer requirements, and a time saving of more than 50 percent in some cases. Reduced inventories result in additional cost savings in logistics and storage.
The management team at Humbel Zahnräder AG had set out the goal of reducing set-up times by 50 percent within one year. It was not possible to achieve this goal with internal resources and the existing level of methodological expertise. The decision was made to contact Ingenics.
For Humbel, it was not mainly a financial matter that triggered the optimization project, but the realization that minimizing time to output was necessary in order to stand up to international comparison. After all, the company has to compare its performance against the competition and its own branches in other countries. Nevertheless, the explicit goal is to offer greater value for money than international competitors despite high labor costs in Switzerland.
For complex set-up processes, it is necessary to have the correct amount of materials and tools at the right time, and the quality has to be right. This affects machine operators and setters as well as employees in quality assurance, production control, and tool service in addition to internal suppliers and, most of all, the logistics department. The workload of these parties can be significantly optimized through the integrated planning, control, allocation, and monitoring of processes.
Since long-term success requires the full cooperation of all departments, one of the first tasks of a workshop is to demonstrate the appeal of the measures in their totality. If factors such as parallel operations, more reliable processes, and optimized routes reduce set-up times by a significant margin, it is possible to bring down batch sizes, logistics costs, and storage capacity by up to 60 percent. While this calls for a large number of individual measures, major investments are not usually necessary.
Once the consultant had become familiar with the objectives, production processes, and equipment of the company, there followed a preliminary assessment with reference to a benchmark and an initial statement concerning concrete potential. The preliminary study indicated that a target of 50 percent was realistic. Then, in a series of set-up workshops, the machinery was prepared for a potential analysis. As a trained toolmaker, industrial foreman, and technical business manager, Ingenics project director Stefan Meitinger was able to inspire participants in the workshop to strive for a common goal. The first step was a 5S workshop that facilitated action to simplify the work system, reduce working distances, and streamline work spaces. The initial results of this were impressive. Spontaneously, an additional layout workshop was arranged when it became clear that the floor plan could easily be optimized without any major effort or expense.
As in all rationalization projects, one crucial element for success was to support employees affected as well as the management team in the development of ideas and their implementation. Managers at Humbel praised the straightforward cooperation, noting that all of their expectations had been met and the apparent potential realized. Measures directed at workstations alone made it possible to reduce average set-up times by about 50 percent, and the use of video analysis achieved an additional 35 percent reduction. The roll-out rate was greatly improved thanks to improved communication between company directors, project management, and staff.
Another important goal was the qualification of engineers, technicians, and machine operators as internal trainers. Their task is now to monitor the sustainability of measures and to transpose results to other systems.